線束加工行業每年因設備操作不當引發的事故占比達32%(數據來源:2023年制造業安全白皮書),這個觸目驚心的數字直指裁線機安全操作的重要性。作為線材加工的核心設備,裁線機在提升生產效率的同時,其高速運轉的刀片、復雜的傳動系統都暗藏安全隱患。本文將深入解析裁線機操作的完整安全體系,助您構建零事故的生產環境。
一、操作前的”三重防護”原則
1. 人員資質認證體系
操作者必須持有《裁線設備操作資格證》,接受不少于16課時的理論+實操培訓。重點掌握設備結構原理(如圖1所示)、應急處理流程、電氣安全知識。建議每季度進行復訓考核,確保知識持續更新。
2. 設備預檢七步法
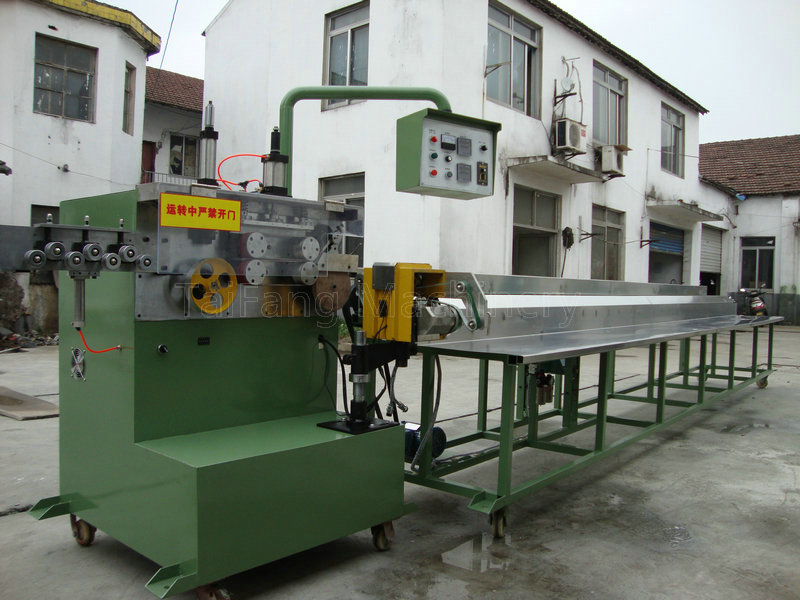
- 刀具安裝狀態:確認上下刀片間隙≤0.02mm且平行度誤差<0.05mm
- 氣壓系統檢測:0.5-0.7MPa工作壓力,儲氣罐排水閥無積液
- 緊急制動測試:連續觸發急停按鈕3次,響應時間<0.5秒
- 傳送帶張緊度:單邊按壓下沉量控制在3-5mm范圍
- 光電保護裝置:遮擋感應器時設備應立即停機
- 電源線路檢查:接地電阻≤4Ω,無線頭
- 廢料收集系統:確保碎屑箱容量<80%
3. 個人防護標準化
*必須佩戴*防割手套(EN388標準4級)、護目鏡(ANSI Z87.1認證)、防靜電工裝。長發者需使用防纏繞發網,嚴禁穿戴領帶、手鏈等易卷入物品。
二、運行中的”五嚴禁三必須”準則
? 五大操作禁令
- 禁止超負荷運行:連續工作2小時需停機15分鐘散熱,線徑處理能力不得超過設備標稱值的120%
- 禁止手動送料:必須使用氣動/液壓輔助送料裝置,手部與刀口距離保持≥15cm
- 禁止參數篡改:刀片轉速、進給速度等核心參數須經工藝工程師雙重確認
- 禁止跨工序操作:調試、維修、清潔等不同作業需切換對應工作模式
- 禁止帶病運行:出現異響(>85dB)、震動異常(振幅>0.1mm)立即停機報修
? 三項必備操作
- 雙人確認制:更換模具時必須執行”操作者+班組長”雙重確認流程
- 實時監控:運用IoT傳感器監測刀具溫度(預警值60℃)、電機電流波動(±15%)
- 定置管理:工作臺面只保留當班物料,工具按TPM標準定位擺放
三、設備維護的”生命周期管理”
1. 日常保養三時段
- 班前:用無水乙醇清潔光電傳感器,潤滑導軌(ISO VG32潤滑油)
- 班中:每2小時檢查刀具磨損量(千分尺測量,允許磨損0.03mm/8h)
- 班后:使用真空吸塵器清理鐵屑,刀片涂防銹油膜(厚度2-5μm)
2. 預防性維護計劃
建立基于設備運行數據的預測性維護模型(見表1):
| 部件 | 維護周期 | 關鍵指標 |
|————-|———-|————————|
| 主軸軸承 | 2000h | 徑向游隙<0.01mm |
| 伺服電機 | 5000h | 絕緣電阻≥100MΩ |
| 氣動元件 | 季度 | 泄漏率<0.1L/min |
四、突發狀況應急處理流程
1. 卡料處置四步法
①切斷氣源/電源 → ②鎖定能量隔離裝置 → ③使用專用退料工具 → ④完整記錄事件經過
2. 工傷應急包配置
包含止血帶(CAT Gen7)、防割傷敷料、斷指保存冰盒(維持4℃)、雙語急救指南
五、環境安全管理要點
- 照明強度:加工區≥500lux,調試區≥300lux
- 噪聲控制:配備隔音罩使操作位噪聲<80dB(A)
- 通風系統:保證換氣次數≥15次/小時,粉塵濃度<3mg/m3
通過構建”人-機-環”三位一體的安全防護體系,某線束廠實施新規程后,設備故障率下降67%,工傷事故實現全年零發生。這印證了科學化、標準化操作規范的核心價值。
TAG: